Safety Protocols for Operating Overhead Cranes in Industrial Settings
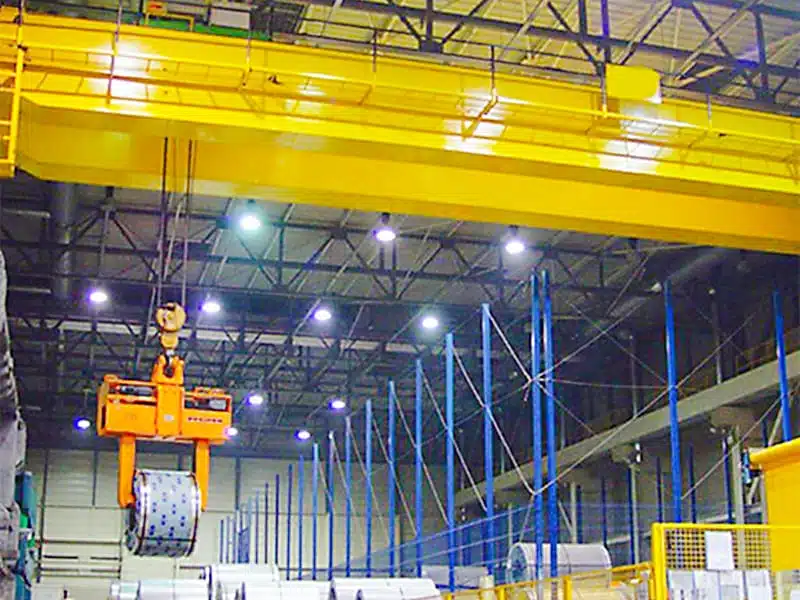
Overhead cranes are essential pieces of equipment in many industries, such as manufacturing, construction, and shipping. They are designed to handle heavy lifting and material movement in environments where manual lifting would be impractical or dangerous. However, like any heavy machinery, overhead crane come with inherent risks. Ensuring the safety of workers and equipment is paramount, not only to prevent injuries but also to protect the integrity of the materials being handled.
In this article, we will explore the best safety protocols and practices for operating overhead cranes in industrial settings. From understanding the crane’s components to proper training and routine inspections, these guidelines will help maintain a safe working environment and improve operational efficiency.
1. Proper Training and Certification for Operators
One of the most critical safety protocols is ensuring that operators are properly trained and certified to handle overhead cranes. Crane operation requires specialized skills, and without adequate training, operators may not be fully aware of the potential hazards and how to avoid them.
Key Training Aspects:
-
Crane Operation Techniques: Operators must be familiar with all aspects of crane operation, including how to maneuver the crane, control the load, and safely move materials. They should also understand how to use all control systems, including emergency stop features.
-
Load Capacities: Understanding the crane’s load limits is vital to prevent overloading, which could lead to equipment failure or accidents. Operators should always be aware of the weight of the load being lifted and ensure it is within the crane’s safe working capacity.
-
Hazard Awareness: Operators need to be able to recognize common hazards associated with crane operations, such as swinging loads, overhead obstructions, and unstable loads. They should also be trained to respond appropriately in emergency situations.
-
Signal Communication: Clear communication between the crane operator and ground personnel is crucial to prevent accidents. Operators should be trained to understand hand signals or radio commands used for guiding crane movements.
Regular certification and recertification programs are essential to ensure operators remain up-to-date on the latest safety procedures and crane technologies.
2. Pre-Operational Inspections
Before operating an overhead crane, it is essential to conduct a thorough pre-operational inspection to ensure that the equipment is in good working condition. This step can help identify potential issues that may compromise safety during operation.
Key Areas to Inspect:
-
Hoist and Hook: Check the hoist mechanism for smooth operation, and inspect the hook for signs of wear or damage, such as cracks or deformations. A damaged hook can cause loads to drop unexpectedly.
-
Cables and Chains: Inspect the lifting cables and chains for fraying, wear, or corrosion. Worn cables can break under load, leading to catastrophic accidents.
-
Trolley and Bridge Systems: Verify that the trolley and bridge mechanisms are functioning properly and that there are no obstructions along the track. Ensure that the crane can move smoothly across its range.
-
Safety Devices: Check that all safety devices, such as limit switches, emergency stop buttons, and overload protection systems, are working correctly.
-
Brakes: Ensure the crane’s braking system is responsive and in good condition. Malfunctioning brakes can lead to uncontrolled movements of the crane, which can be dangerous for both the operator and nearby workers.
By conducting a thorough pre-operational inspection, operators can identify and address any issues before they pose a safety risk.
3. Proper Load Handling
Handling loads properly is crucial to maintaining crane safety. Overhead cranes are designed to lift heavy materials, but improper loading techniques can create hazardous situations, such as dropped loads or crane instability.
Best Practices for Load Handling:
-
Ensure Proper Load Rigging: Always ensure the load is properly rigged before lifting. Use slings, hooks, and other lifting accessories that are in good condition and rated for the weight of the load. The load should be securely attached to avoid any shifting or falling during movement.
-
Check the Load Balance: Loads should be evenly distributed to avoid tipping or swinging. If the load is unbalanced, it can cause the crane to sway or tip, leading to accidents or equipment damage.
-
Do Not Overload the Crane: Every crane has a maximum load capacity, and it is critical to adhere to these limits. Overloading the crane can lead to equipment failure, including the collapse of the crane or broken cables. Always ensure that the total weight of the load does not exceed the crane’s rated capacity.
-
Avoid Swinging Loads: Swinging loads can be dangerous, especially in tight spaces. Operators should raise the load slowly and steadily and avoid sudden movements. When transporting a load, move it at a controlled speed to minimize swinging.
Using the proper load-handling techniques will ensure that materials are moved safely and efficiently, reducing the risk of accidents.
4. Maintaining Clear Communication
Clear communication is essential for crane operations, especially when the operator cannot see the entire area where the load is being moved. Ground personnel or signalers should maintain constant communication with the crane operator to guide movements, signal when to lift or lower the load, and ensure there are no obstacles in the crane’s path.
Communication Guidelines:
-
Use Hand Signals or Radios: Ground personnel should be trained in hand signals or use radios to communicate effectively with the crane operator. Clear, consistent signals help avoid misunderstandings and ensure that movements are coordinated.
-
Establish Communication Protocols: Before beginning a lift, establish a communication protocol. Ensure everyone involved in the operation knows what signals or radio calls will be used, and make sure that there is no confusion during the lifting process.
-
Maintain a Safe Distance: Ensure that all personnel, including the crane operator, are positioned at a safe distance from the lifting area. Workers should avoid standing directly under or near the load during lifting operations.
Maintaining clear communication between the crane operator and other personnel helps to coordinate movements and reduces the risk of accidents or injuries.
5. Regular Maintenance and Inspections
Routine maintenance and inspections are essential for ensuring the long-term safety and reliability of overhead cranes. Regular checks help identify potential issues before they develop into significant problems that could compromise safety.
Key Maintenance Considerations:
-
Lubrication: Ensure that all moving parts are regularly lubricated to prevent wear and tear that could lead to malfunction.
-
Replacement of Worn Parts: Monitor components such as cables, chains, and hoists for signs of wear. Worn or damaged parts should be replaced immediately to prevent accidents.
-
Electrical Systems: Regularly inspect electrical systems to ensure they are functioning properly. Faulty wiring or control systems can lead to operational failures.
-
Structural Inspections: Overhead cranes often operate under extreme conditions, and regular structural inspections are necessary to ensure that beams, runways, and supporting structures remain in good condition.
By establishing a regular maintenance schedule and adhering to it, companies can ensure that their cranes are functioning at peak safety levels and reduce the likelihood of unexpected failures.
6. Using Proper Personal Protective Equipment (PPE)
When working with overhead cranes, safety is the top priority. Workers should be equipped with appropriate personal protective equipment (PPE) to ensure their safety during crane operations.
Recommended PPE:
-
Hard Hats: To protect workers from falling objects.
-
Steel-Toed Boots: To safeguard against injuries from dropped materials or equipment.
-
High-Visibility Clothing: To ensure workers are visible to crane operators and other personnel.
-
Gloves: To protect hands from sharp edges or hot surfaces when handling loads.
PPE should be worn by all personnel involved in crane operations, especially those who are working in close proximity to the crane or the load being lifted.
7. Emergency Procedures
Finally, it is essential to have clear emergency procedures in place in case of an accident or malfunction. Operators should be familiar with emergency protocols and know how to respond if an incident occurs.
Key Emergency Protocols:
-
Emergency Stop Procedures: Operators should know how to immediately stop the crane in case of an emergency to prevent further damage or injury.
-
First-Aid Training: Ensure that personnel are trained in basic first aid and are equipped with necessary medical supplies in case of an injury.
-
Evacuation Plans: Establish and communicate clear evacuation procedures in case of fire, equipment failure, or other emergencies.
Having well-established emergency procedures helps minimize the impact of an accident and ensures a quick, efficient response when necessary.
Conclusion
Operating overhead cranes safely in industrial settings requires strict adherence to safety protocols and best practices. From proper training and load handling to regular inspections and clear communication, every aspect of crane operation plays a vital role in maintaining a safe working environment. By following these safety guidelines, businesses can reduce the risk of accidents, improve efficiency, and protect workers and equipment, ensuring that crane operations run smoothly and securely.
Investing in safety is not only critical for compliance with regulatory standards but also for protecting the well-being of workers and the integrity of industrial operations. By fostering a culture of safety, companies can enhance their productivity while minimizing the risks associated with crane operations.